How Advanced CNC Machining and Custom Solutions Solve High-Precision Manufacturing Challenges for Telescope Components
Client Need Overview
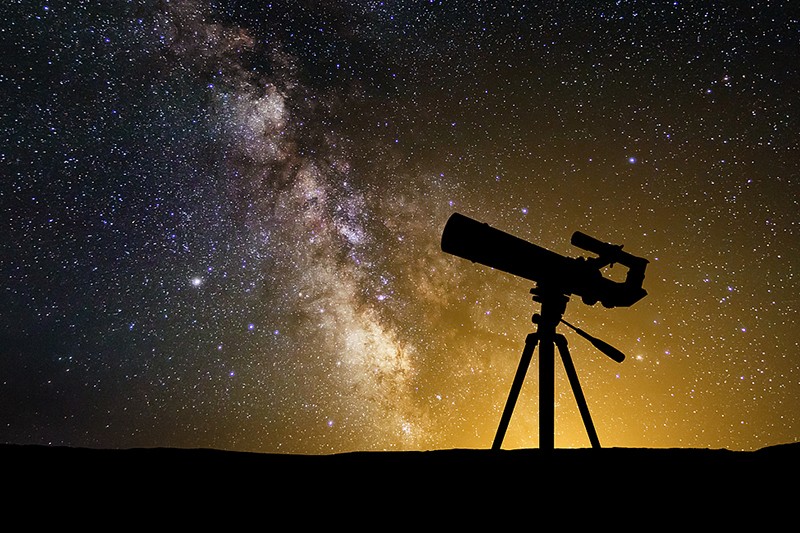
Selestron, LLC, a leading provider of telescopes and optical products, is renowned for its innovative technology in the field of astronomy. With increasing demand for high-quality optical systems, Selestron requires precision-machined parts to maintain product excellence. The company’s key needs revolve around producing telescope parts with high precision, complex geometries, and short lead times.
Project Description
Selestron's manufacturing requirements involved producing complex telescope components that meet high-performance standards while adhering to strict tolerances. The main challenges included:
Precision Requirements: Parts required tight tolerances to ensure perfect alignment in optical systems, impacting overall performance.
Complex Materials: Telescope components often need to be made from lightweight yet durable materials, such as aluminum alloys and specialized composites, which pose challenges in machining and surface treatment.
Efficient Production: Given the fast-paced consumer demand, Celestron needed a solution that not only ensured precision but also optimized production timelines.
The project’s primary goal was to overcome these challenges by implementing advanced machining technologies and improving manufacturing efficiency.
Solution and Implementation Process
To meet Selestron's stringent requirements, our company implemented the following approach:
Advanced CNC Machining: We used state-of-the-art CNC equipment capable of handling the tight tolerances required for telescope parts. This technology enabled precise milling, turning, and drilling, ensuring that each component met the necessary specifications.
Custom Tooling and Materials: We employed customized tooling to handle the unique geometries of telescope parts, and selected high-quality aluminum and composite materials to balance weight, strength, and durability. The use of aerospace-grade materials guaranteed the parts' reliability and performance.
Surface Treatment and Coating: To protect the parts from environmental factors, we applied specialized coatings and surface treatments. These ensured durability, reduced friction, and improved the parts' longevity.
Streamlined Production Process: We optimized the production workflow using lean manufacturing principles. This included reducing cycle times, minimizing waste, and improving inventory management to meet the client’s short lead time requirements.
Quality Control: Each batch of parts was rigorously tested for precision and performance. Using coordinate measuring machines (CMM) and other advanced inspection techniques, we ensured that every component met or exceeded Celestron’s quality standards.
Results and Outcomes
The project resulted in the following achievements:
Enhanced Precision: CNC machining allowed us to achieve a production tolerance of ±0.002mm, ensuring perfect alignment and function of telescope components.
Improved Production Efficiency: By streamlining the manufacturing process, we reduced lead times by 25%, allowing Selestron to meet market demands more effectively.
Cost Optimization: By optimizing the machining process and using high-quality, cost-efficient materials, we were able to reduce production costs by 15%, delivering a cost-effective solution without compromising on quality.
Customer Satisfaction: Celestron was highly satisfied with the quality, precision, and timely delivery of the components. The improvements in production efficiency and cost reduction allowed them to offer better pricing and faster delivery to their customers.
Customer Feedback
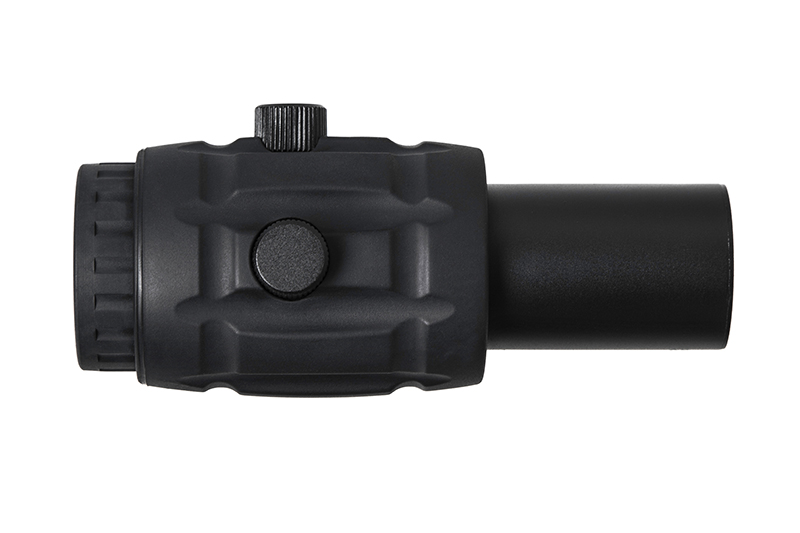
John Smith, Senior Manufacturing Manager, Selestron, LLC.
"We are extremely pleased with the results of this partnership. The precision and quality of the telescope components are top-notch. The timely delivery and cost savings have significantly improved our product offerings, and we look forward to future collaborations."
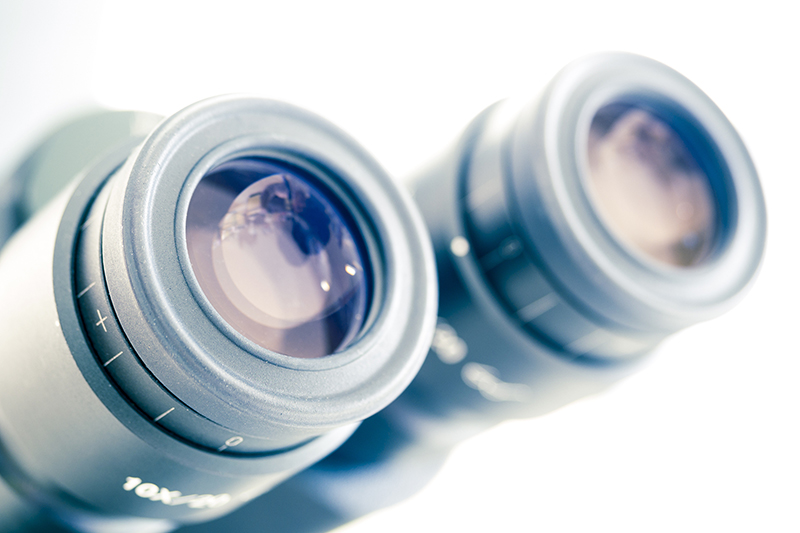
Senior Engineer at Selestron
“We’ve been impressed with the precision and efficiency demonstrated by Xiamen Prime Kunwu Industrial. The new telescope parts perform flawlessly, and we’ve seen substantial cost reductions in production. Their ability to meet our high standards in both engineering and delivery was a key factor in our decision to continue partnering with them.”
Conclusion & Contact Us
This case study highlights our ability to deliver high-precision solutions for complex manufacturing challenges. Our expertise in CNC machining, combined with our commitment to quality and innovation, allows us to provide tailored solutions for industries like astronomy, optics, and more.
If your company is facing similar challenges, we invite you to contact us for a consultation and discover how we can help optimize your manufacturing processes.
Contact us today to learn more about our precision solutions.
FAQs
Q1: What types of materials are commonly used in telescope manufacturing?
A1: Telescope parts are often made from aluminum alloys and specialized composites for lightweight durability and precision.
Q2: How can CNC machining improve the precision of telescope parts?
A2: CNC machining ensures tight tolerances, achieving precision of up to ±0.002mm for critical parts like telescope components.
Q3: What is the lead time for telescope parts production?
A3: Lead times are optimized using lean manufacturing principles, reducing production cycles by up to 25%.
Q4: How does surface treatment affect telescope part performance?
A4: Surface treatments reduce friction, protect parts from environmental factors, and improve overall durability.
Q5: What are the main challenges in manufacturing telescope parts?
A5: Key challenges include achieving high precision, handling complex geometries, and working with specialized materials.
Gallery
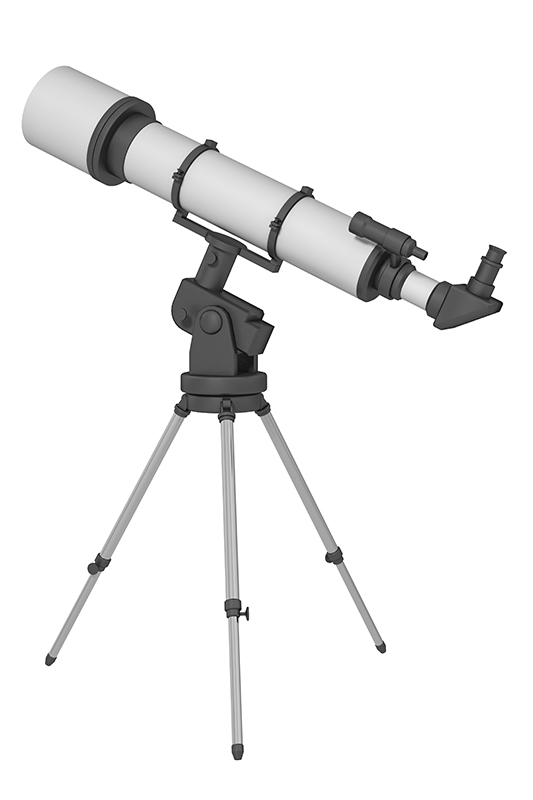
Astrophotography accessories
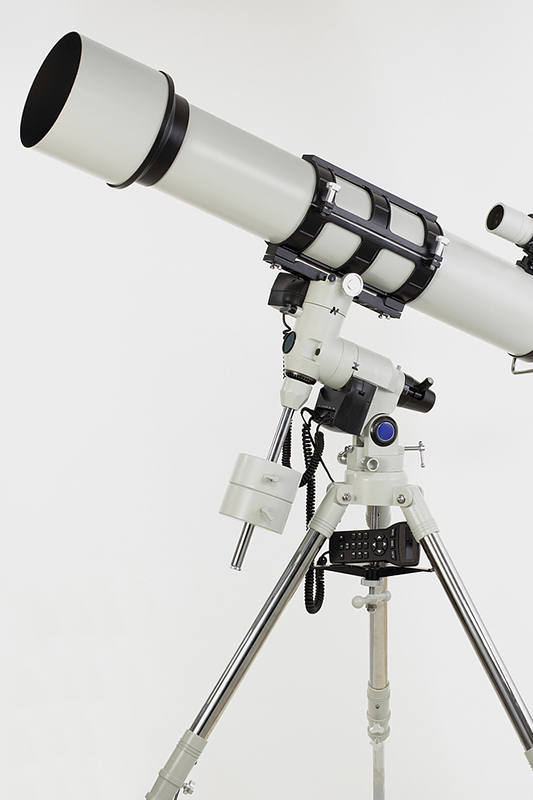
Telescope parts
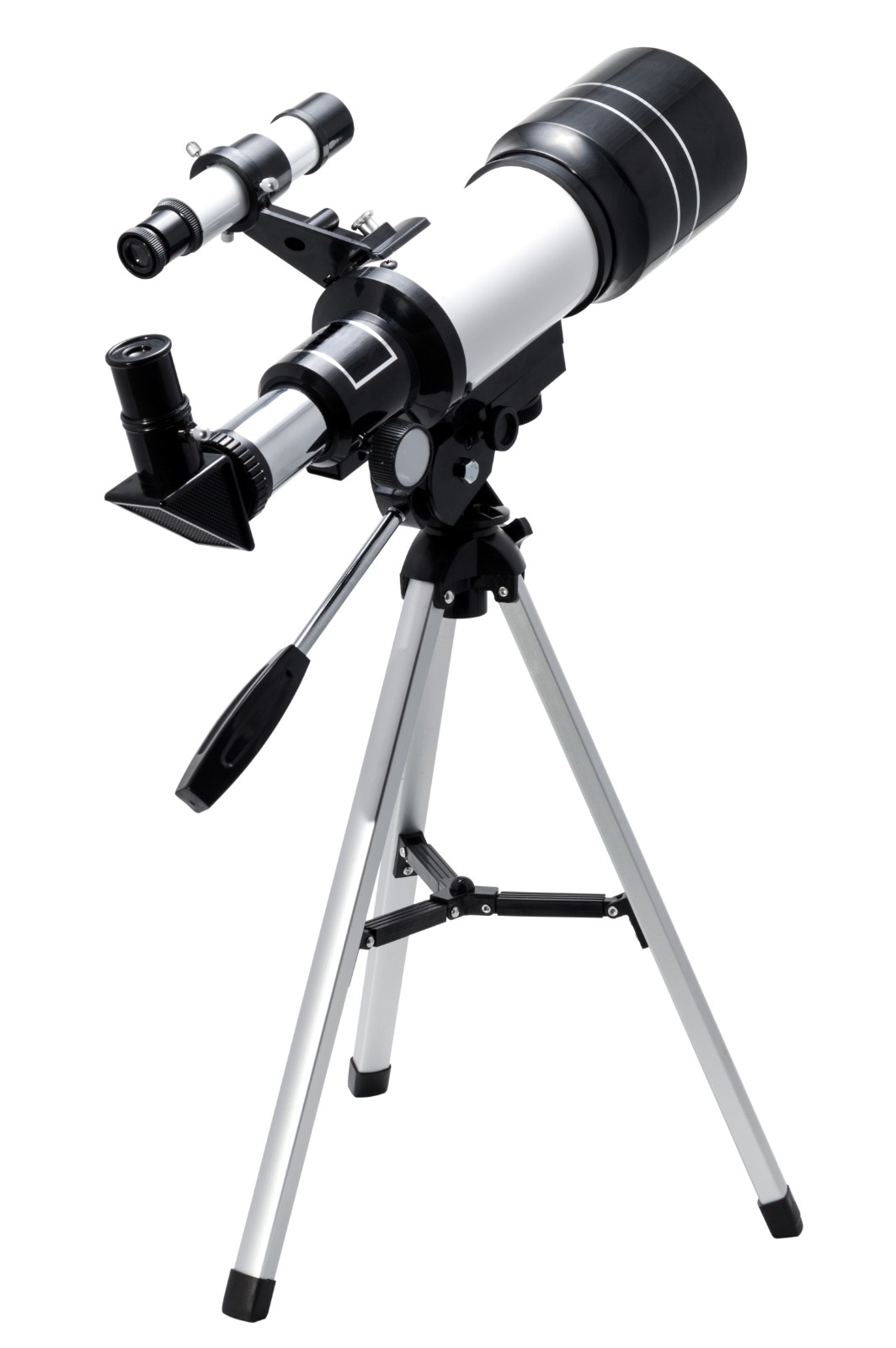
Astronomy accessories
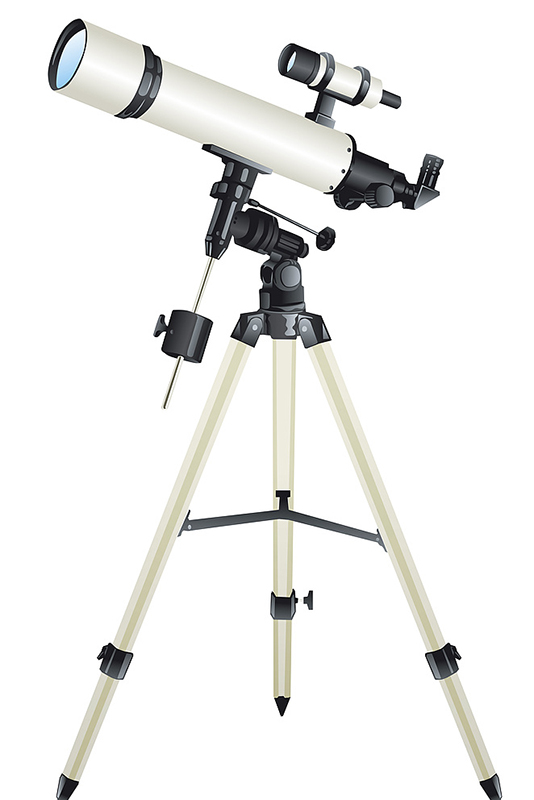
Astronomy accessories
Contact Info
Mr. Brook Lin
Job Title: Sales manager
E-mail: [email protected]
Mob/WhatsApp:+86 13599927066
Wechat:+86 13599927066 Skype:+86 13599927066
Country/Region: China (Mainland) Province/State: Fujian
Operational Address: Building 172, Tongan Industrial Zone, Tongan Area, Xiamen, Fujian, China (Mainland) Zip: 361100