Project Brief
Industry | Innovative aerospace industry |
Product | Aluminum Prototyping for Aerospace Imaging Device |
Challenges | The production of lightweight yet highly durable components. |
Technology | The aluminum prototypes met the required tolerances with a high degree of accuracy. Our machining capabilities ensured that the critical dimensions of the prototypes were within micrometer precision. |
Material | high-strength, lightweight aluminum alloys |
Surface finish | Anodizing and Coating |
Quantity | 100Sets |
Lead Time | 20 Business days |
Client's Needs Overview
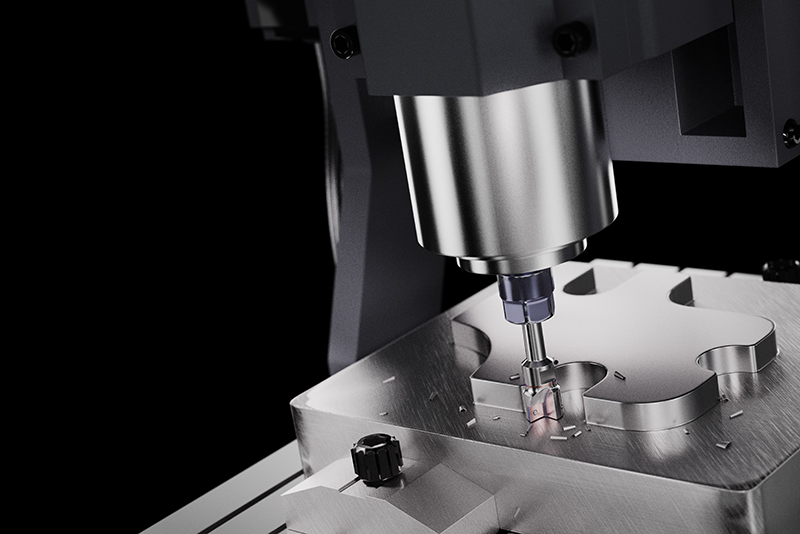
Our client, an innovative aerospace company, specializes in the development of advanced imaging technology for SAR (Synthetic Aperture Radar) aircraft systems. The client was looking for high-precision aluminum prototypes to validate the design of an imaging device that would be integrated into an aerospace application. Given the stringent requirements of the aerospace industry, the project demanded exceptional accuracy and strength, with a focus on optimizing performance while reducing weight.
Industry Challenges and Project Description
The aerospace sector is under constant pressure to innovate, and one of the key challenges lies in the production of lightweight yet highly durable components. For this project, the main hurdles included ensuring the aluminum prototypes met the exacting tolerances required for high-performance imaging, while maintaining structural integrity under demanding environmental conditions. Furthermore, material selection and the complexities of prototype validation in a tight timeline were significant challenges for the project.
The client required precise aluminum prototypes for an aerospace imaging device, needing to meet a series of high-performance criteria, including dimensional accuracy and surface finish. The prototypes were to be used for testing and validating the functionality of the imaging system before the final production phase.
The technical requirements included:
High Precision: The prototypes had to meet very tight tolerances in terms of dimensions and geometric accuracy.
Material Integrity: The selected aluminum material had to perform under stress and varying environmental conditions while maintaining optimal weight-to-strength ratio.
Surface Treatment: The prototypes required specific surface treatments to enhance their durability and functionality under operational conditions.
Solution and Implementation Process
At Xiamen Prime Kunwu Industrial Co., Ltd., we addressed the client’s requirements with a comprehensive solution combining advanced CNC machining and material expertise. Our team focused on delivering high-precision aluminum prototypes using state-of-the-art technology and a thorough understanding of aerospace material requirements.
Material Selection:
After analyzing the project’s needs, we recommended high-strength, lightweight aluminum alloys specifically suited for aerospace applications. This material selection helped balance the need for durability with the weight-saving requirements of the aircraft's imaging system.CNC Machining:
We employed advanced CNC machining techniques to ensure the prototypes adhered to the exact dimensional tolerances required by the client. Our precision machining allowed us to achieve the high level of accuracy necessary for the complex geometry of the imaging device.Surface Treatment:
To enhance the durability of the aluminum parts, we implemented specific surface treatment processes such as anodizing and coating. These treatments provided the prototypes with the required corrosion resistance and enhanced mechanical properties, critical for their use in demanding aerospace environments.Quality Assurance:
We conducted rigorous quality checks throughout the manufacturing process, including dimensional inspections, surface finish evaluations, and mechanical testing to ensure the prototypes met the client’s high standards.
Results and Achievements
Faster Time-to-Market:
Our use of advanced CNC machining allowed us to significantly reduce the time required for prototype production. The client was able to move forward with the validation and testing phase ahead of schedule, which streamlined the overall project timeline.Enhanced Precision:
The aluminum prototypes met the required tolerances with a high degree of accuracy. Our machining capabilities ensured that the critical dimensions of the prototypes were within micrometer precision.Cost Efficiency:
Through our optimized manufacturing processes, we were able to reduce production costs while still maintaining the necessary quality and performance standards.
Customer Feedback
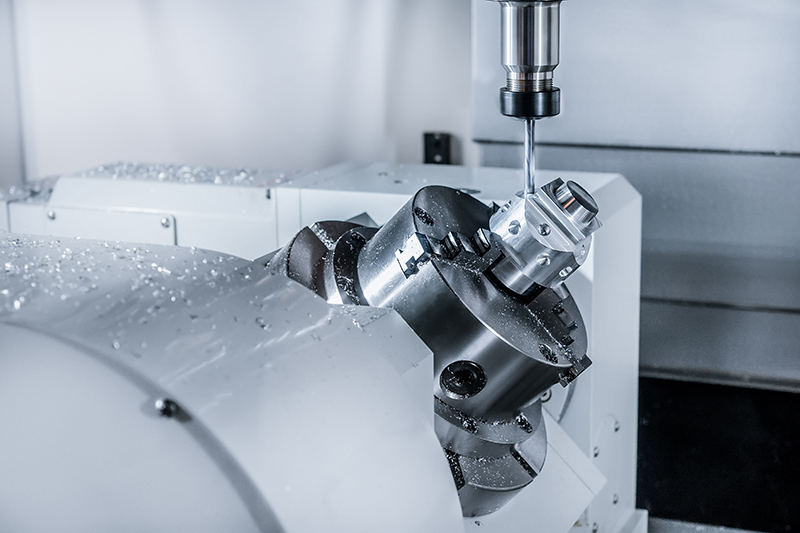
— John Doe, Senior Engineer, AeroTech Solutions
"Xiamen Prime Kunwu’s team delivered exceptional results. Their ability to meet our precise tolerances and deliver high-quality aluminum prototypes on time was critical to our project's success. Their expertise in material selection and surface treatment has significantly improved the performance of our imaging device. We are confident that these prototypes will play a crucial role in the success of our aircraft systems."
Conclusion and Call to Action
This case study highlights the exceptional capabilities of Xiamen Prime Kunwu Industrial Co., Ltd. in providing high-precision CNC machining and material solutions for the aerospace sector. Our ability to solve complex engineering challenges and deliver timely, cost-effective prototypes sets us apart as a leader in the precision machining industry.
If you are facing similar challenges in prototyping or precision machining, we invite you to contact us and explore how we can collaborate to develop customized solutions that meet your exact requirements.